Vibrating mechanical systems assembled from metallic components dissipate energy due to damping. Besides the loss of energy in the material itself especially the join patches contribute to the energy dissipation. As long as the exciting forces do not exceed a certain level, the damping properties are almost linear with respect to the excitation level. In addition, experimental investigations show that the stiffness and the damping properties of materials and joints are nearly frequency independent.
For numerical simulations of the dynamical behavior of structures the finite element method (FEM) has established itself as a powerful tool. Even though the mass and the stiffness distribution of a structure can be modeled within the FEM quite precisely, there is still a lack of suitable damping models. Classical approaches such as the Rayleigh damping result in a high frequency dependency of the damping properties which is in contrast to results from respective measurements. Other approaches such as the use of fractional derivatives are not available within commercial software programs. Another option offered by some FE codes is the ’constant hysteretic model’ which assumes frequency independent damping properties. Since the model leads to non-causal behavior in time-domain calculations it can only be used in the frequency domain where one obtains a complex stiffness matrix. Thus, a modal analysis of a structure which incorporates hysteretic damping in general leads to complex eigenmodes and eigenvectors. Depending on the location of a join patch within a structure, its contribution to the energy dissipation changes from mode to mode. This is why — in contrast to material damping — the damping properties of joints have to be modeled locally.
In the context of noise and vibration harshness (NVH) manufacturers aim in optimizing the acoustical and vibrational behavior of their products even before a prototype is built. Thus, CAD engineers face the problem to accurately model the damping behavior without having suitable tools at hand. As a solution strategy within commercial FE codes, so-called thin-layer elements can be generated at the location of the join patches under consideration. In a next step, the damping properties of the respective joints have to be measured by an appropriate isolated joint experiment. They are then assigned to the thin-layer elements using the model of constant hysteresis.
Two different research projects are addressed to this modelling approach:
- a co-financed project (FVV/DFG) in which special attention to the needs in the automotive industry is paid
- a DFG-project that deals especially with stability considerations of rotating saw blades and respective FE modelling techniques
Publikationen
Ehrlich, C., Schmidt, A. and Gaul, L.: "Modellierung von Fügestellendämpfung in Motoren", ATZ - Automobiltechnische Zeitschrift 118.3, 2016, pp. 68-73
Ehrlich, C., Schmidt, A. and Gaul, L.: "Reduced thin-layer elements for modeling the nonlinear transfer behavior of bolted joints of automotive engine structures", Archive of Applied Mechanics 86:59–64, 2016 , online-journal
Ehrlich, C., Schmidt, A. and Gaul, L.: "Reduced Thin-Layer Element Model for Joint Damping", Proceedings of ICoEV 2015: International Conference on Engineering Vibration, Ljubljana, Slovenia, September 7-10, 2015. pdf
Ehrlich, C., Schmidt, A. and Gaul, L.: "Microslip Joint Damping Prediction Using Thin Layer Elements", Proceedings of IMAC XXXII: A Conference & Exposition on Structural Dynamics, Orlando, FL, USA, February 3-6, 2014, CD-ROM. PDF
Schmidt, A., Bograd, S. and Gaul, L.: "Measurement of join patch properties and their integration into finite-element calculations of assembled structures", Shock and Vibration, 19, 2012, pp. 1125-1133
Bograd, S., Reuss, P., Schmidt, A.., Gaul, L. and Mayer, M.: "Modeling the dynamics of mechanical joints", MSSP 25(8), 2011, pp.2801-2826
Bograd, S., Schmidt, A. and Gaul, L.: "Joint damping prediction by thin layer elements", Proceedings of IMAC XXVI: A Conference & Exposition on Structural Dynamics, Orlando, FL, USA, February 4-7, 2008, CD-ROM. PDF
Kontakt
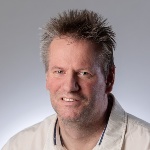